Keep Your Surface Grinder Running Smoothly
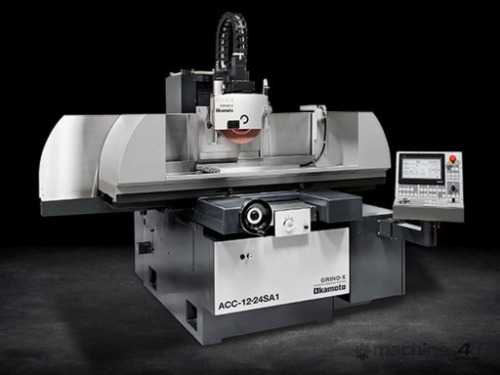
Regular maintenance is crucial for any machinery, but it is especially vital for precision tools like surface grinders. These machines usually have a hydraulic system that includes components such as cylinder rods, hydraulic pumps, lube pumps, pressure gauges, and filters. Neglecting proper care can lead to increased downtime, expensive repairs, and compromised work quality. On the other hand, a well-maintained grinder ensures consistent production of accurate, high-quality parts.
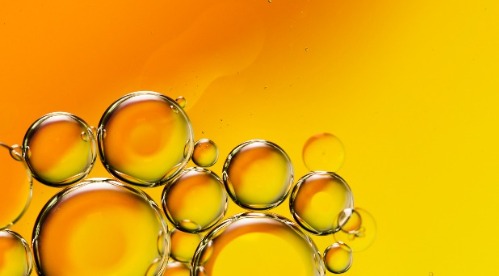
Oil and Filter Service
Contaminated oil is a common issue in surface grinders. Coolant, wheel grit, and grinding debris can mix with the oil, reducing its effectiveness and potentially damaging the machine. Regular oil changes help prevent these issues and keep your machine
running smoothly.
Steps to Perform Oil and Filter Service
- Drain the Oil: Start by draining the old oil from the machine.
- Remove the Old Filter: Take out the used filter.
- Clean the Reservoir: Clean the oil reservoir thoroughly to remove any contaminants.
- Install New Oil and Filter: Refill the machine with new oil and install a fresh filter.
- Check and Adjust Hydraulic Pressure: After replacing the oil, check the main hydraulic pressure
gauge and adjust it to factory specifications if necessary.
.png)
Electrical Checks
Regular electrical inspections are essential for maintaining the functionality and longevity of your
machine's electrical components.
Key areas to check include:
- DC Power Supplies: Ensure they are functioning correctly.
- Motor Amperage: Check for any irregularities.
- Solenoid Coil Ohms: Verify the resistance levels.
- AC Drive Voltage and Step-down Transformers: Make sure they are operating within the required parameters.
Proper electrical maintenance can help prevent electrical surges and extend the lifespan of these components.
Machine Leveling and Chuck Grinding
Keeping your machine level is critical for maintaining factory accuracy throughout the life of the V-ways. Regular leveling checks can prevent downtime caused by inaccurate part grinding.
Grinding the chuck surface prevents inaccuracies caused by corrosion and grinding debris buildup. This maintenance step ensures a smooth and accurate table surface, essential for producing precise parts.
Other Important Checks and Tips
Hydraulic Pressure
Maintaining proper hydraulic pressure is crucial for the optimal operation of your surface grinder. Regularly check the main hydraulic pressure gauge and adjust it if it's not within factory specifications. This simple step can go a long way in preventing issues related to hydraulic system performance.
Lube Flow and Drain
Proper lubrication is vital for extending the lifespan of mechanical components such as ball screws,
V-ways, and slideways. Regular checks of the lubrication system ensure that these parts receive adequate lubrication, reducing wear and tear.
Guards Off Cleaning
Removing guards for thorough cleaning helps prevent contamination of oil and mechanical components. This practice also prevents guard binding, damage, and corrosion, ensuring smooth operation and longer machine life.
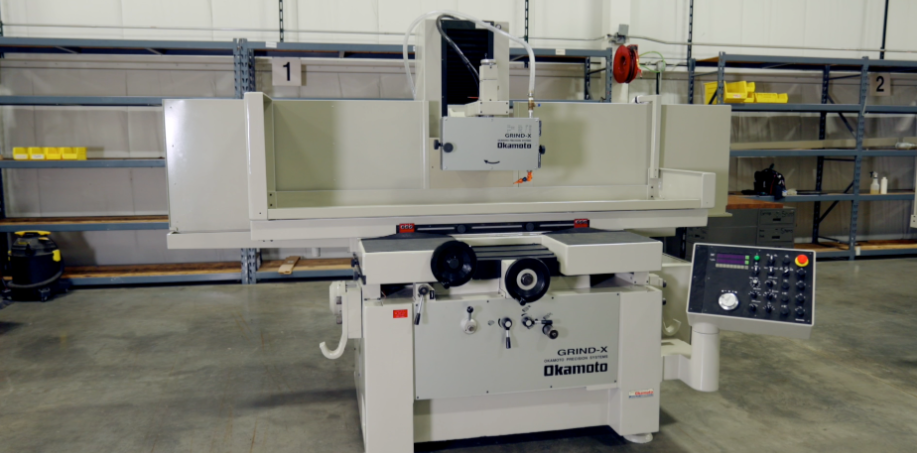
Signs It's Time to Schedule a PM
- Fluid Leaks: Look for oil or coolant leaks around the machine.
- Damaged or Missing Guarding: This can create safety issues and lead to contamination.
- Inaccurate Part Tolerances: If your machine can't produce accurate parts, it's time for a check-up.
- Insufficient Part Finish: This could be due to many things such as unbalanced grinding wheel, worn spindle bearings, or wheel dressing issues.
- Using Incorrect Oil: Always use factory-recommended premium oil to prevent sticking valves and premature solenoid failure.
- Using Compressed Air or Wash Down Hoses: This can lead to forced contamination.
- Leaving the Machine On: Avoid leaving your machine on overnight or during holiday breaks to prevent electrical surges and reduce the lifespan of electrical components.
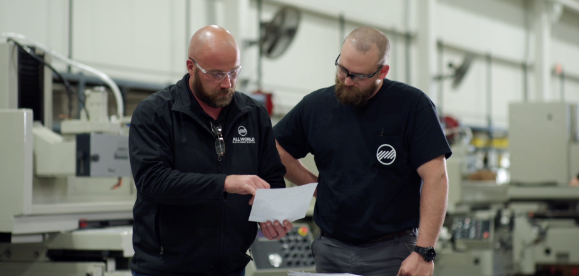
Regular maintenance is vital for keeping your surface grinder in top working condition. By following the recommended steps and scheduling yearly or biannual preventive maintenance checks, you can ensure optimal machine performance, minimize downtime, and boost productivity.
To simplify your maintenance routine, consider partnering with a reliable service provider. Titan Machinery Sales, an All World Machinery Supply Group company, offers comprehensive annual preventive maintenance schedules to keep your grinder in excellent shape. Contact us today to schedule your next maintenance service and ensure smooth operations. Our expert technicians, with decades of experience servicing surface grinders, can get a machine serviced in a day or less.